Я отправился в гости к своему старому другу, который работает в дизайн-бюро Опеля в Рюссельсхайме, и прогулялся по цехам завода, где производят автомобили Инсигния и Астра. И еще я узнал, откуда пошла поговорка «Каждый автомобиль когда нибудь становится Опелем».
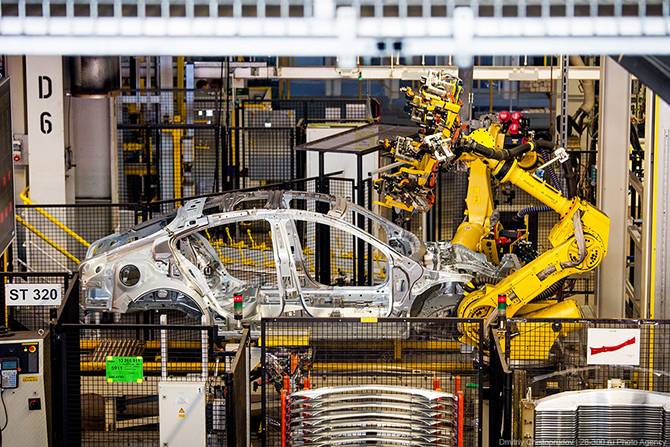
Завод Опеля является градообразующим предприятием в Рюссельсхайме. Здесь находится штаб-квартира Opel Haus. Многие ошибочно считают, что слоган Опеля переводится как «Мы любим автомобили», но правильный перевод — «Мы живем автомобилями».
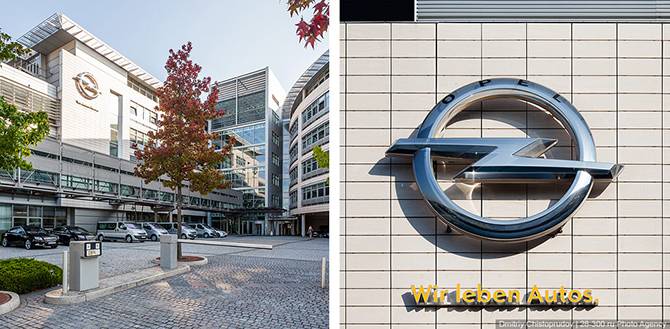
Сначала я подумал, что это демонстрационные электромобили, но оказалось что они рабочие — высшее руководство передвигается на Амперах, которые днем заряжаются рядом с входом в здание. Я уже давно думаю прокатиться на Ампере по Европе. В Россию такие автомобили не поставляются, так как нет необходимой инфраструктуры, и наши мозги еще не готовы заботиться об окружающей среде, как это делают в Европе или в США.
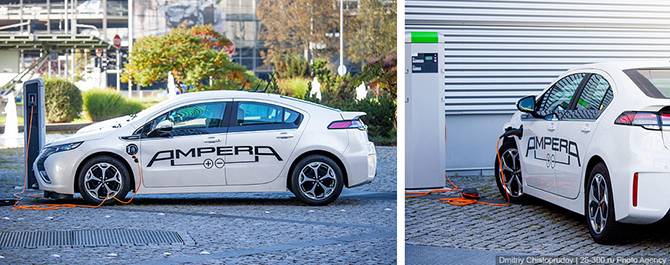
Само здание оснащено хитрой системой климат-контроля, которая автоматически открывает и закрывает форточки, регулирует наклон жалюзи, что позволяет экономить энергию на отоплении и работе кондиционеров.
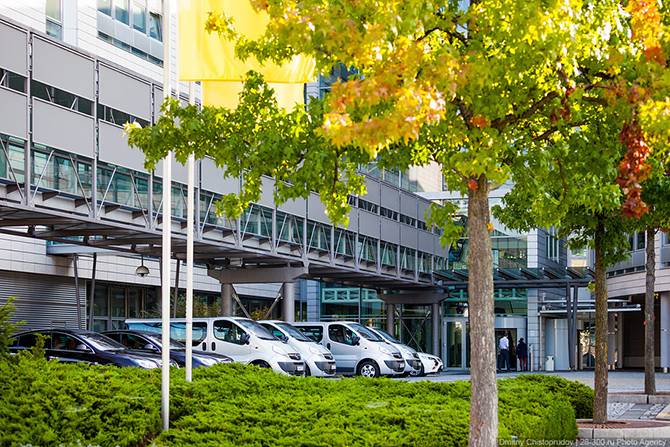
Часть электроэнергии для офисов вырабатывается солнечными батареями.
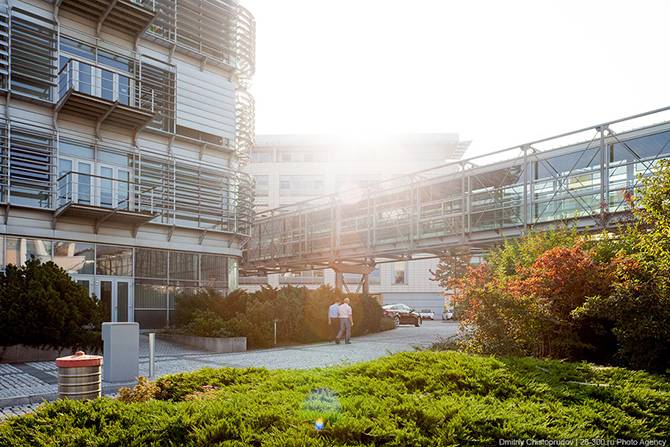
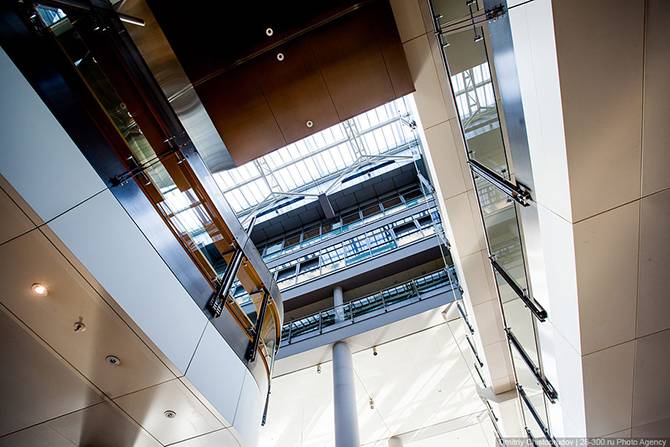
Первый в мире самолет с ракетным двигателем RAK1 до сих пор находится в воздухе под крышей Опель Хауса. На нем 30 сентября 1929 года Фриц фон Опель совершил свой полет в окрестностях Франкфурта.

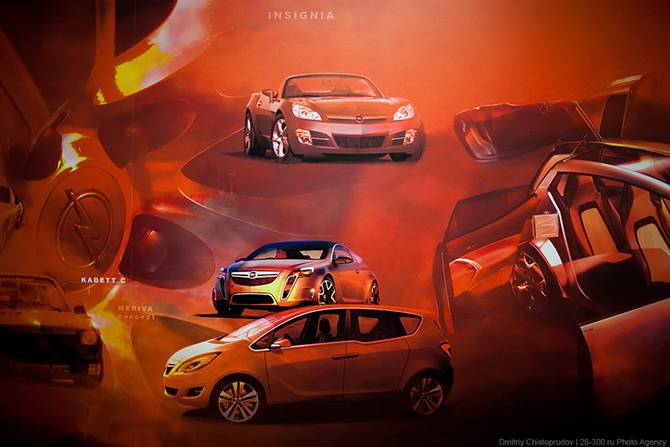
Встретились старые друзья, которые 6 лет просидели за «одной партой». Андрей Гусев работает креативным дизайнером по экстерьеру автомобилей в отделе перспективных разработок (Advanced Design). Он ведет работы над созданием концепт-каров автомобилей Опель. Также Андрей участвовал в разработке дизайна новой Астры.
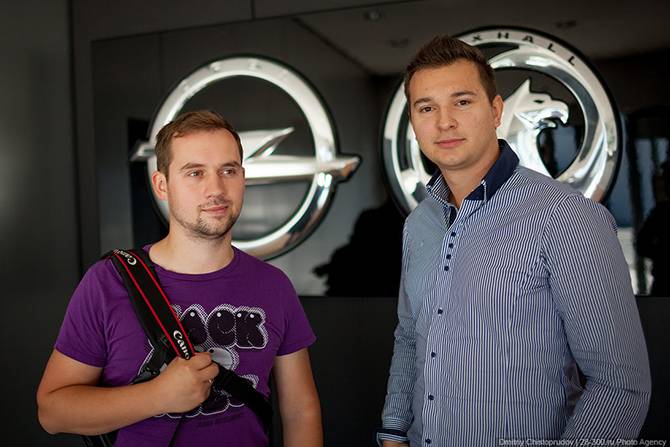
Перед прогулкой по заводу, мы зашли в Visualisation Room. Этот зал используется для различных презентаций, совещаний по проектам и обсуждению виртуальных моделей.
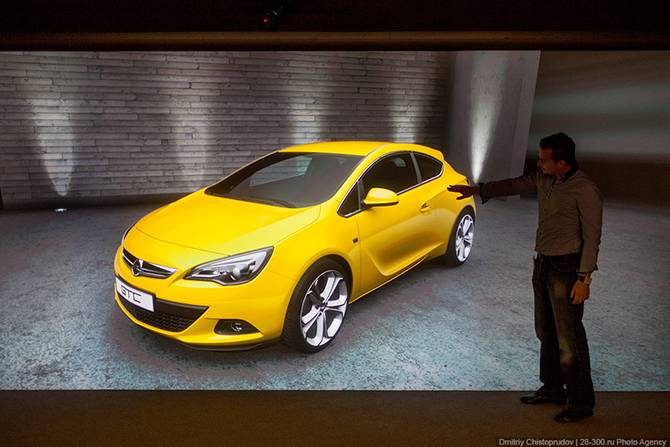
На специальном экране размером во всю стену проецируется изображение автомобиля в натуральную величину, что упрощает восприятие и оценку объекта на начальных стадиях разработок.
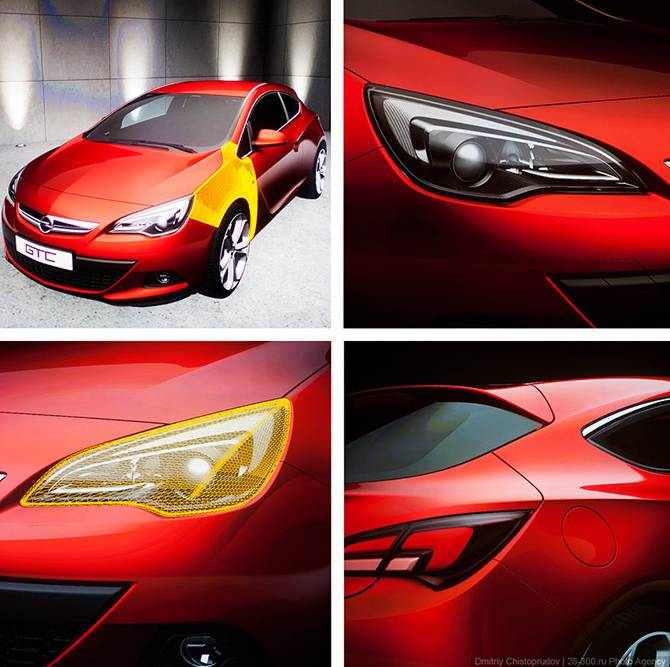
Также здесь ведутся переговоры с другими студиями GM по всему миру (США, Корея, Австралия, Бразилия) — это как Скайп, только не перед компьютером, а в кинотеатре. Именно в этой комнате принимаются решения о том, какая модель пойдет или не пойдет в серийное производство.
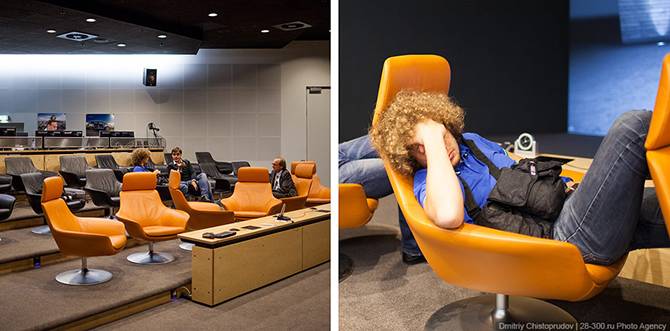
В 1863 Адам Опель открыл в Рюссельсхайме фабрику по производству швейных машин, сейчас здесь один из крупнейших и старейших автозаводов в мире. Здесь работает 16000 человек и ежегодно выпускается 180000 автомобилей.
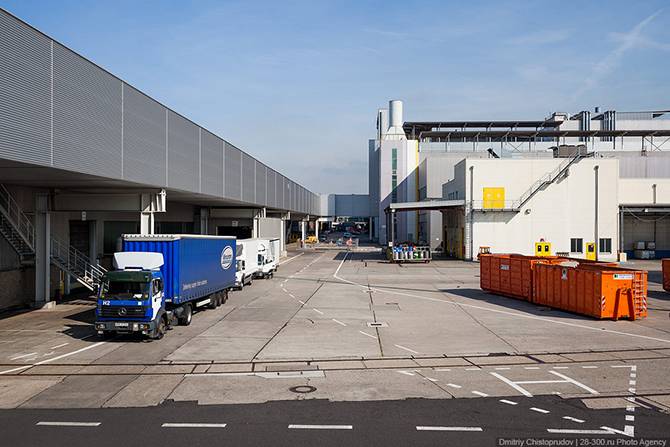
Крупнейший кузнечный (штамповочный) цех Опеля. Во время работы прессов пол немного дрожит, как во время маленького землетрясения. С виду рулоны бумаги, а на деле — стальные листы для кузовных деталей.

Более плотные листы поставляются паллетами. После Второй Мировой войны с металлом была напряженка, и для производства автомобилей Опель использовали металлолом, переплавленный из старых автомобилей. Отсюда-то и пошла поговорка «Каждый автомобиль когда-нибудь становится Опелем».
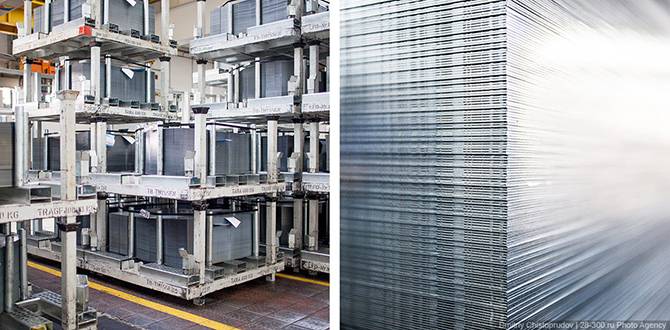
Кузнечные прессы.
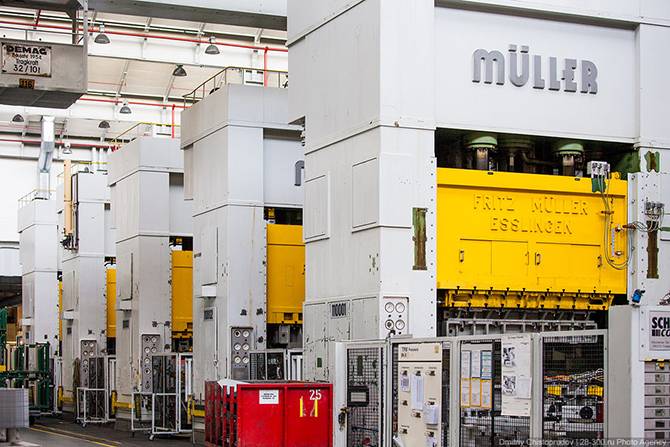
На заводе кругом немецкий порядок. Технический проход поделен на три части — для тележек, перевозящие матрицы для прессов (оранжевая конструкция слева), зона для движения погрузчиков и другой техники, и дорожка для велосипедистов и пешеходов.
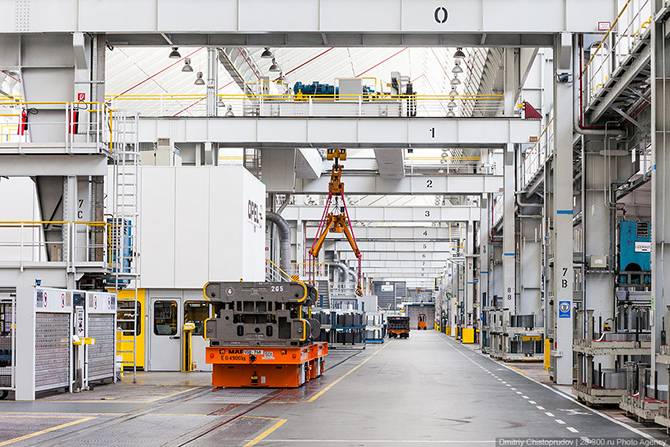
Огромные матрицы, которые устанавливают в прессы для штамповки различных кузовов и элементов.
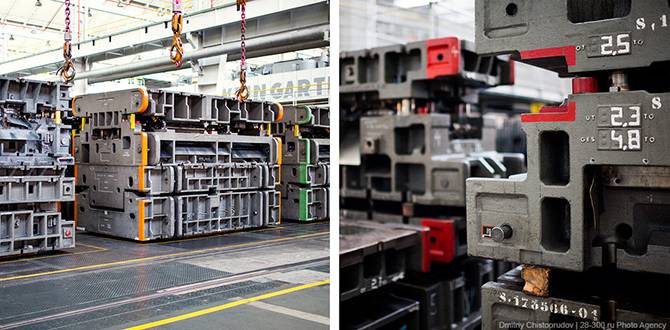
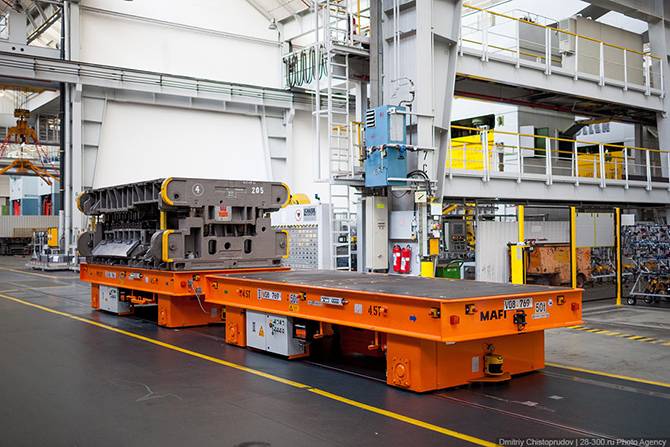
Сотни матриц рассредоточены по всей площади цеха. Все они промаркированы разными цветами в соответствии с своей моделью автомобиля.
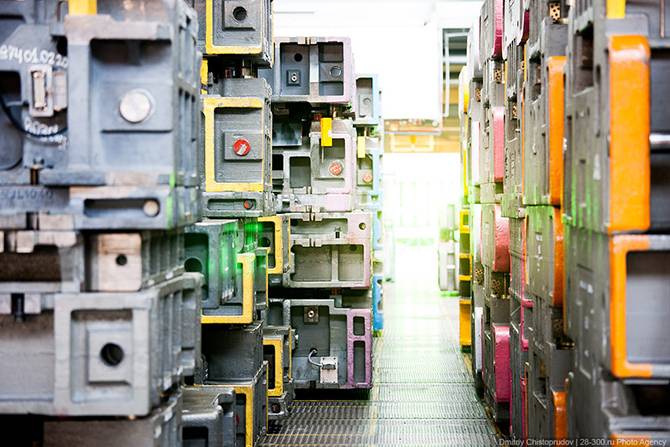
В кузнечном цеху люди выполняют только функцию контроля качества.
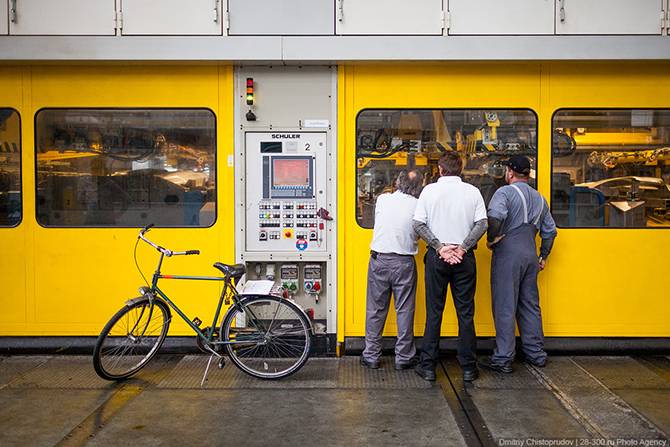
Прессы работают громко и быстро. Никаких фотографов, которые пытаются сделать резкий кадр, они не ждут.
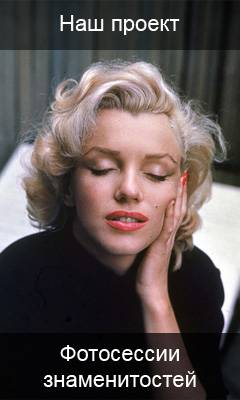
Этот станок штампует до двадцати маленьких форм в минуту.
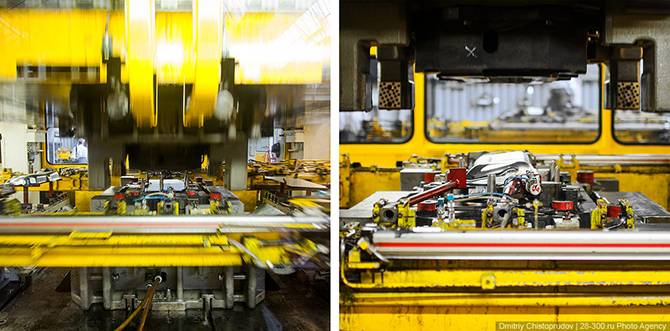
Такой станок стоит 40 миллионов евро. За одну операцию он штампует боковину автомобиля. Пресс весит 6500 тонн.
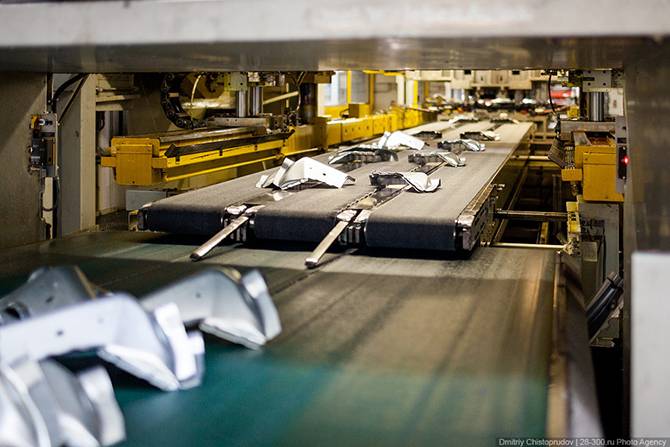
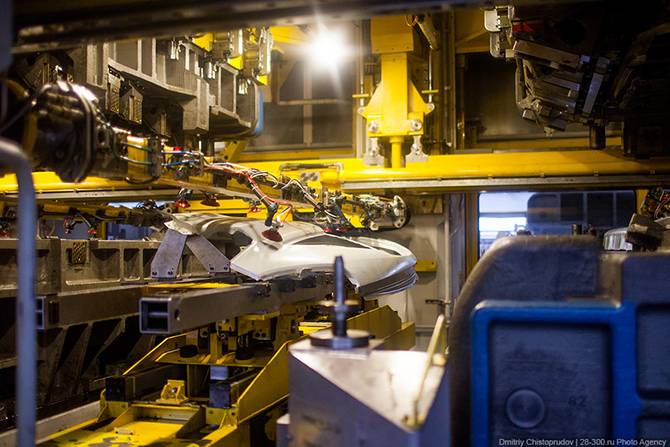
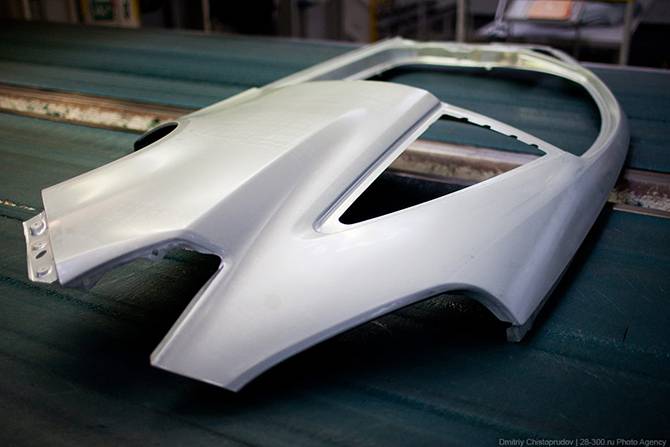
Готовые детали отправляют на сварку и окраску.
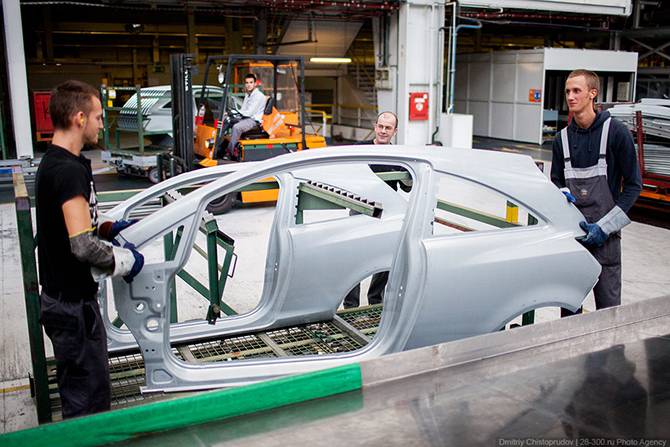
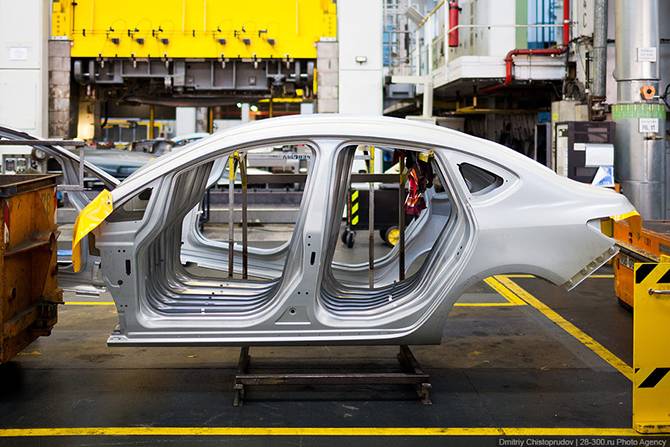
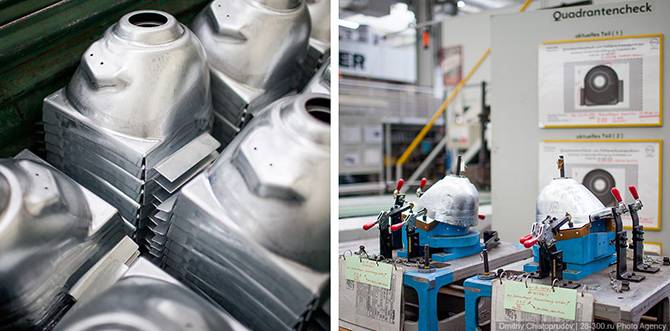
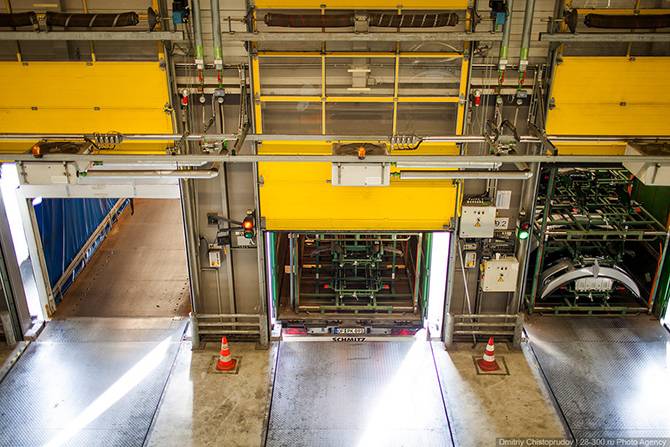


Сварочный цех работает в две смены. В каждой смене 200 человек.
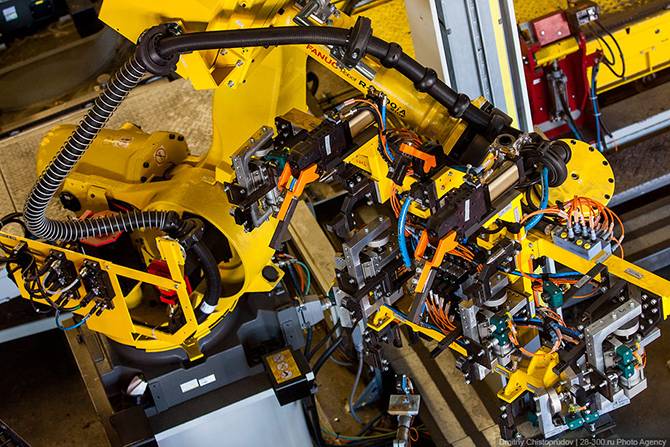
На сварке и сборке кузова работают 700 роботов, каждый из которых стоит по 100 тысяч евро. Производство автоматизировано на 98%.
Голый кузов весит 400 кг, а на покраску уходит 8 кг краски и лака. К сожалению, снять процесс покраски не разрешили.
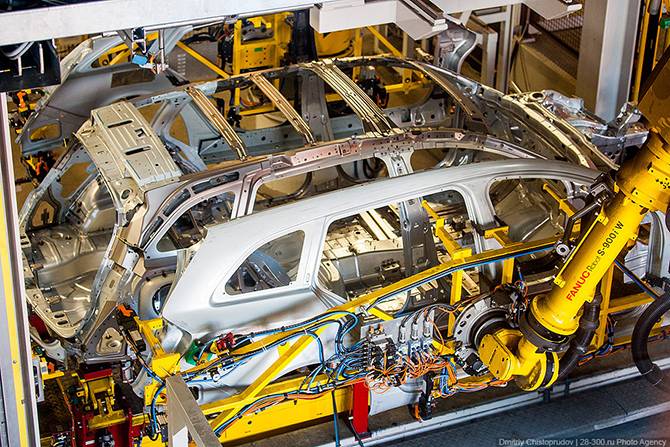
В цехе сборки работает 2000 рабочих в две смены. Они работают в группах по 5 человек. В этом цеху специальный такт времени – 65 секунд. За 65 секунд рабочий должен сделать определенный этап работы. Если он не успевает — конвейер останавливается. Везде есть специальные веревочки, дернув за которые, конвейер останавливается, и начинает играть музыка. У каждой бригады своя мелодия, по ней бригадир устанавливает, у кого проблема и помогает быстрее ее решить.
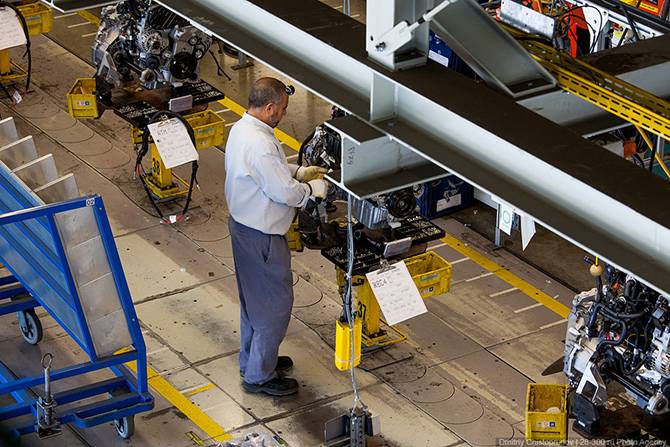
Всего на конвейер подается до 40 видов моторов.
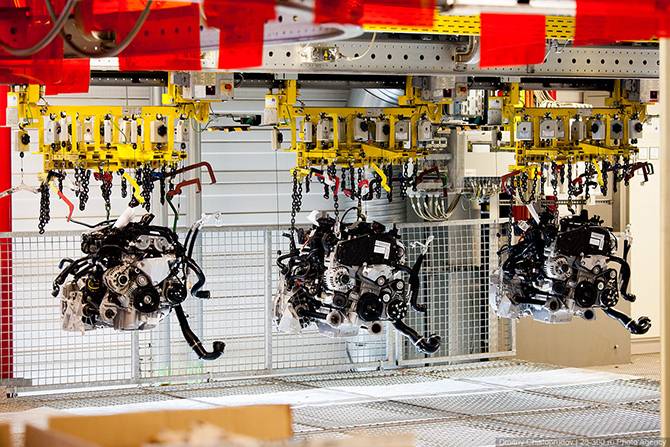
Я раньше был уверен, что есть, допустим, конвейерная линия по выпуску желтой Лады Калины, седан с двигателем 1.6, автомат. Линия работает несколько месяцев, потом ее изменяют и выпускают другие автомобили. А в Опеле на одной конвейерной линии собираются одновременно друг за другом разные автомобили разной комплектации и конфигурации. Компьютер следит, чтобы каждый мотор, каждая деталь кузова, нашли именно свою машину.
Для меня это было открытием дня. На одном конвейере можно выпускать до 9 разных моделей машин!
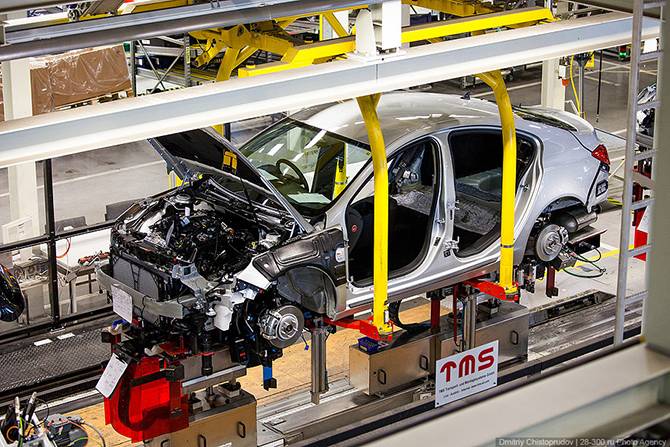
Если очень захотеть, можно приехать на завод и посмотреть, как собирается именно ваш автомобиль.
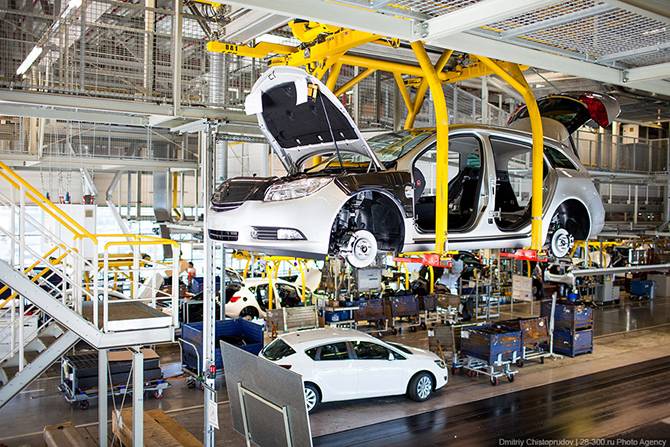
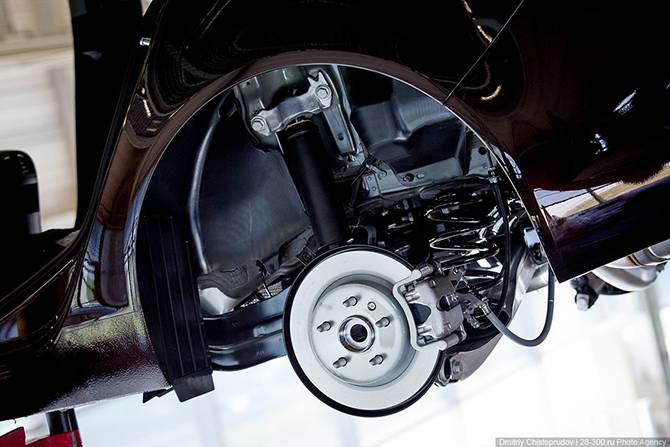
Все автомобили проходят ряд испытаний на герметичность кузова, управляемость, торможение, работу основных элементов.
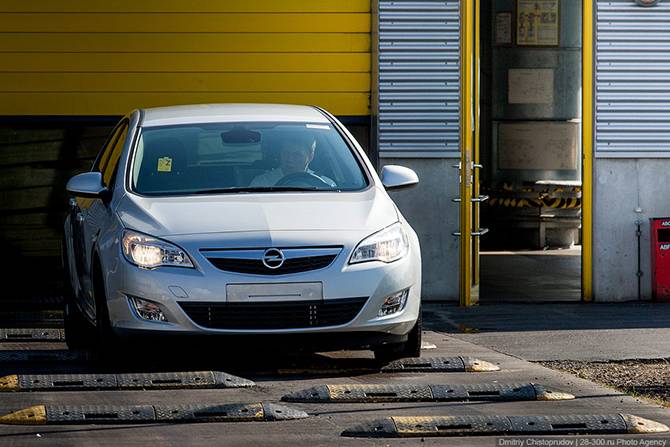
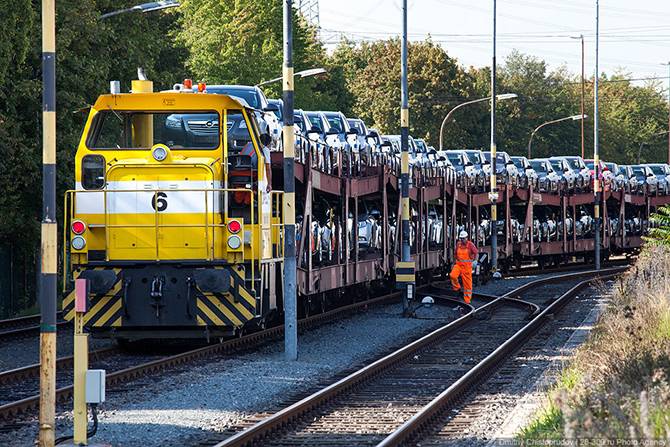
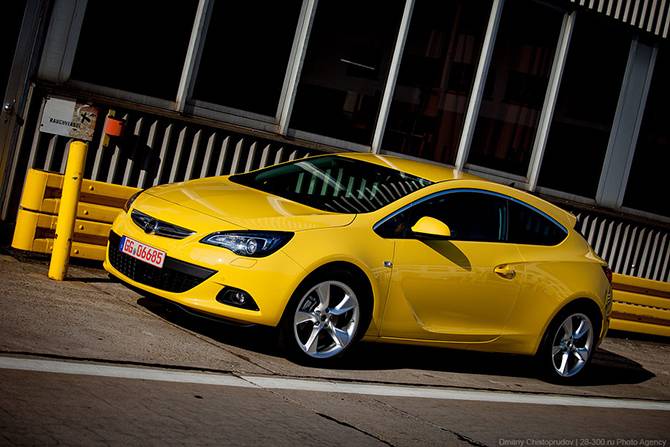
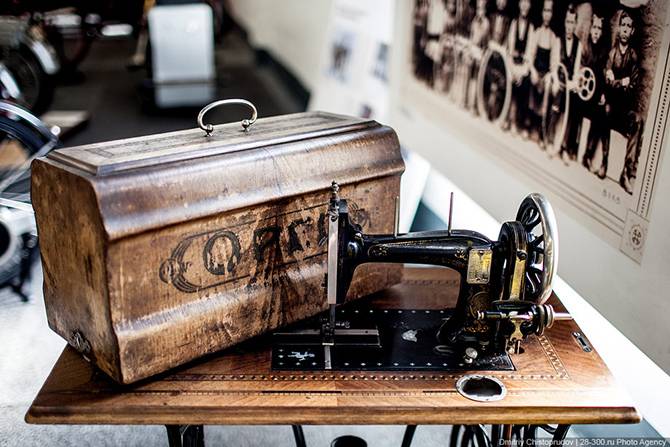
В музее представлены автомобили из разных эпох. Сам музей больше напоминает мастерскую. В нем постоянно ведется работа по реставрации экспонатов. Площадь не позволяет разместить все экспонаты, поэтому больше половины коллекции хранится в запасниках. Через несколько лет музей переедет в новое помещение.
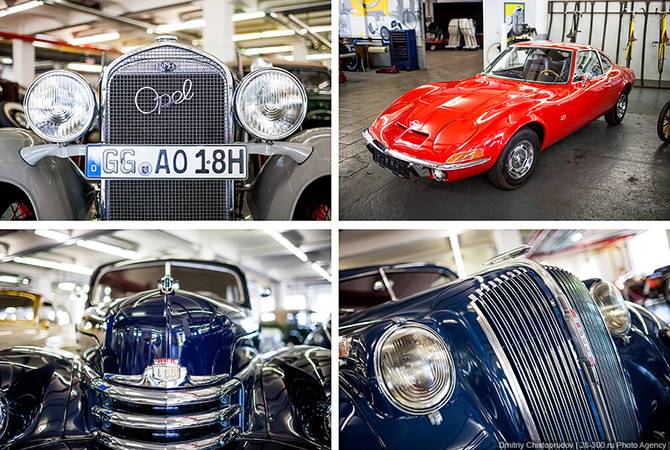
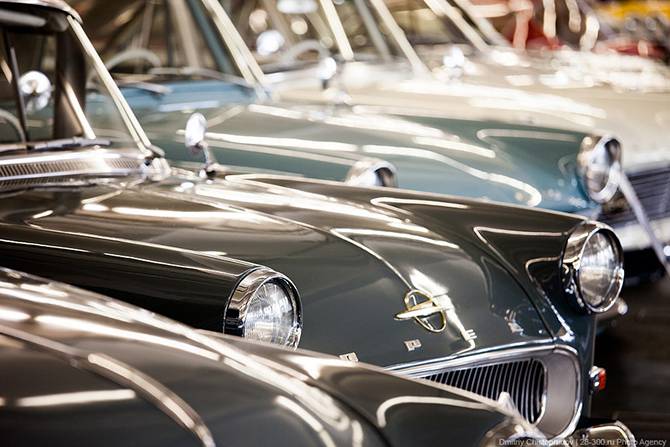
В запасниках хранятся концепт-кары. Это, например, концепт Антары.
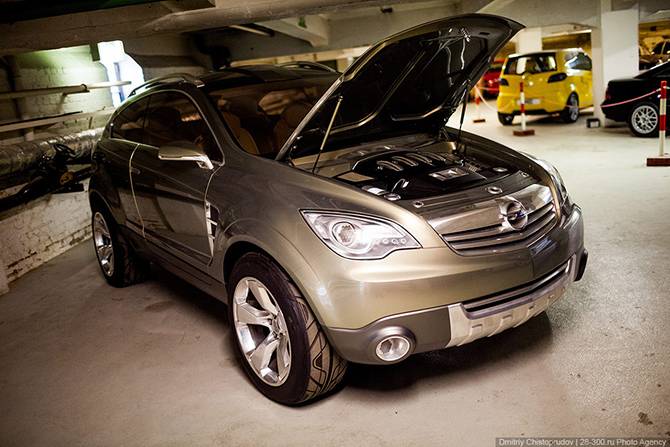
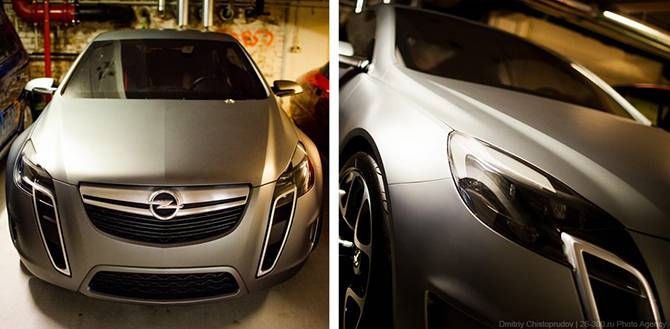
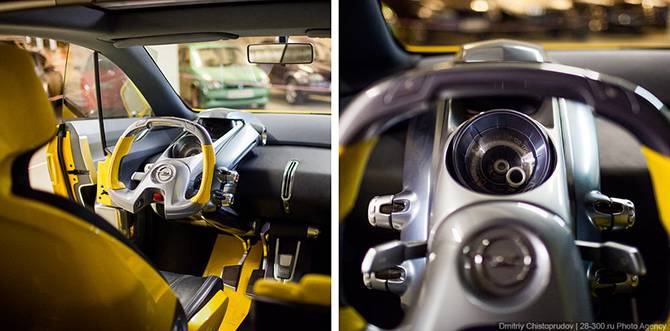
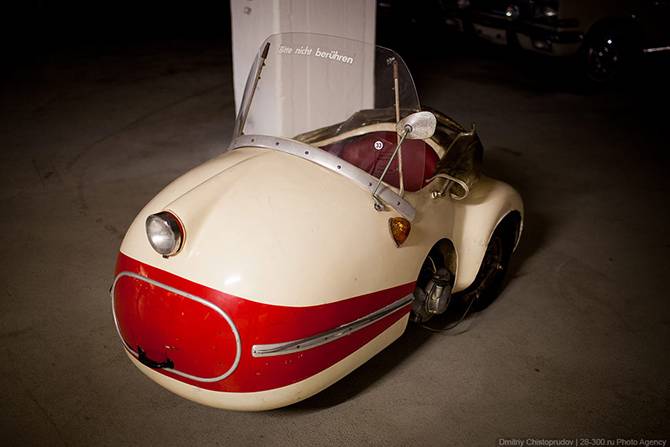
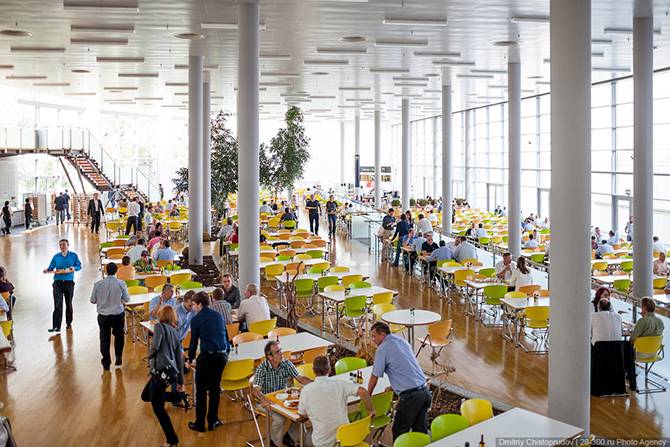